在工業(yè)中,激光技術(shù)的使用飛快增長,激光加工占金屬加工年度總收入的74%,隨著市場需求的不斷增加,超過了過去一年7%。汽車、金屬轉(zhuǎn)化或增材制造是激光加工在工業(yè)領(lǐng)域應(yīng)用的例子,并被廣泛使用。由于激光加工過程參數(shù)不確定,實(shí)時(shí)(RT)監(jiān)控是激光加工研究的一個(gè)重大課題。
激光加工過程中造成產(chǎn)品缺陷的主要原因是熱動(dòng)力學(xué)、溫度和熱循環(huán),因?yàn)樗鼈儧Q定材料不希望的脆性相和殘余應(yīng)力,這些影響可能會使構(gòu)件的力學(xué)行為受損,導(dǎo)致產(chǎn)品加工失敗。熱分布和熔池(激光熔覆)的幾何尺寸或小孔(激光焊接)是其監(jiān)測的關(guān)鍵參數(shù),通過控制這些參數(shù)來確保激光加工的產(chǎn)品質(zhì)量。
基于激光的設(shè)備實(shí)現(xiàn)將靈活性、生產(chǎn)率、精度和零缺陷生產(chǎn)結(jié)合,這是一項(xiàng)重大挑戰(zhàn)。為了提高產(chǎn)品質(zhì)量,增加生產(chǎn)產(chǎn)量,基于激光加工過程需要新的在線實(shí)時(shí)監(jiān)控系統(tǒng),新的激光源和加工頭正向增強(qiáng)通用性和復(fù)雜性演變,允許修改不同過程參數(shù),如激光調(diào)制、自適應(yīng)聚焦等。實(shí)現(xiàn)全自動(dòng)化和零缺陷制造過程的新方法將需要智能焊接頭,該智能焊接頭將激光器、光學(xué)器件、執(zhí)行器、傳感器和電子器件集成在一個(gè)緊湊而經(jīng)濟(jì)的設(shè)備上,該設(shè)備的最終目的能夠處理:
1、不斷增加的過程復(fù)雜性
2、不斷增加的精度和可靠性要求
3、不斷增加的自治、重構(gòu)和自診斷要求
新紅外傳感器的發(fā)展有助于將零缺陷概念引用到工業(yè)激光制造過程中。
低成本高速紅外成像傳感器
激光制造過程產(chǎn)生的許多缺陷來自激光加工動(dòng)力學(xué)不穩(wěn)定,當(dāng)明確需求,滿足新一代監(jiān)控系統(tǒng)應(yīng)用于激光制造過程中,溫度和時(shí)間響應(yīng)是要考慮的關(guān)鍵參數(shù)。
在激光切割過程中,熔化的材料液滴必須從切縫噴出,以避免渣和積渣,它的形成和分離所需要的時(shí)間要小于0.5ms。就激光焊接過程而言,孔內(nèi)擾動(dòng)會產(chǎn)生焊縫小孔,擾動(dòng)的振蕩時(shí)間要小于0.7ms。鍍層、修復(fù)或增材激光制造使用了激光熔覆技術(shù),在無控激光熔覆過程中熔池尺寸變化1%的時(shí)間要小于200ms。使用選區(qū)激光熔化(SLM)技術(shù)進(jìn)行增材激光制造,它所需要的時(shí)間為0.13ms,用于改變激光聚焦位置,變化的距離等于聚焦半徑,所以在這段時(shí)間內(nèi)發(fā)生的任何擾動(dòng)將會導(dǎo)致缺乏精確性或在最后部分產(chǎn)生氣孔。在增材制造過程中,孔隙、空隙、松散粉末的形成和未熔透很依賴溫度變化過程,如冷卻和加熱速率,它對加工過程的關(guān)鍵部分影響很大。
監(jiān)測系統(tǒng)的采樣頻率必須是擾動(dòng)現(xiàn)象造成缺陷頻率的兩倍,因此,為監(jiān)測大多數(shù)激光制造過程,采樣頻率需要高達(dá)10kHz?,F(xiàn)今,基于激光加工過程的大多數(shù)工業(yè)監(jiān)測系統(tǒng)使用基于硅的相機(jī)(VIS-VNIR),將相機(jī)耦合到標(biāo)準(zhǔn)的基于單點(diǎn)紅外探測器的非接觸式溫度系統(tǒng),對焊縫區(qū)進(jìn)行實(shí)時(shí)的溫度測量。這些類型的系統(tǒng)提供的信息不充分,是平均、空間和時(shí)間的結(jié)果,采集的紅外信號僅用了一個(gè)傳感器,失去了溫度分布和熱動(dòng)力學(xué)的相關(guān)信息,更重要的問題是涉及到目標(biāo)運(yùn)動(dòng)或聚焦距離,會經(jīng)常出現(xiàn)錯(cuò)誤(即不可用)的測量結(jié)果。
基于高速紅外成像傳感器的解決方案能夠同時(shí)提供熱動(dòng)力學(xué)信息和空間分布信息,然而,高靈敏度紅外傳感器歷來與高成本掛鉤,通常超出行業(yè)標(biāo)準(zhǔn)范圍。而低成本紅外技術(shù)如微測輻射熱計(jì)或熱釋電器件在響應(yīng)速度方面不能滿足要求,另一方面,量子紅外探測器的響應(yīng)速度是足夠快,但由于其復(fù)雜性和技術(shù)成本,在過去這一行業(yè)中,它們的使用受到限制。幸運(yùn)的是,今天紅外技術(shù)的發(fā)展和低成本高速紅外成像傳感器已成現(xiàn)實(shí)。最近新紅外技術(shù)(NIT)公司已經(jīng)使第一量子中波紅外成像傳感器商業(yè)化,該傳感器單片集成Si-CMOSROIC,提供的圖像分辨率低,非制冷運(yùn)行時(shí)的幀速為10kHz,與傳統(tǒng)點(diǎn)探測器的成本相同。該技術(shù)可以被認(rèn)為是突破性的技術(shù),滿足市場發(fā)展研究所預(yù)見的需求,該研究針對激光加工,如增材制造、焊接和鍍層。
激光焊接過程
激光焊接技術(shù)被廣泛應(yīng)用在大的產(chǎn)業(yè),如汽車、金屬加工、航空航天等。激光焊接技術(shù)有望替代傳統(tǒng)焊接技術(shù)是當(dāng)今的趨勢。就效率、可重復(fù)性和維護(hù)而言,激光焊接技術(shù)相比于其他焊接技術(shù)的優(yōu)勢是明顯的。然而,激光焊接也有一些缺點(diǎn),可能出現(xiàn)焊接缺陷,如洞穴、氣孔、未焊透和飛濺,這根本原因大多與連接過程中所涉及的復(fù)雜機(jī)制有關(guān)。為了避免這些缺陷,需要對激光焊接過程進(jìn)行正確的參數(shù)化,如激光功率、焊接速度、焦距、保護(hù)氣體流和橫向位置,通過控制這些參數(shù)可以獲得更好的焊接質(zhì)量。像激光光斑的幾何形狀、表面清潔時(shí)的光和物質(zhì)之間相互作用問題、材料質(zhì)量與材料組成以及接觸面積,這些參數(shù)也都直接影響焊接質(zhì)量。因此,需要更好的、改進(jìn)的控制系統(tǒng),該系統(tǒng)要統(tǒng)籌考慮動(dòng)力(原因)和焊接區(qū)產(chǎn)生的熱動(dòng)力學(xué)及空間分布(影響)問題。
有幾個(gè)特征信號與激光焊接過程相關(guān),如果激光束的輻射能量足夠熔化金屬,將激光束聚焦在或聚焦到工件的表面,在熔化的金屬里會形成小孔,這小孔有助于熔池的金屬蒸發(fā)。焊接過程的主要信號來自熔池的紅外輻射,次要信號包括等離子體(主要在可見光和紫外線區(qū))和聲波輻射,大多數(shù)焊接監(jiān)測方法至少檢測出以上一種信號。就這項(xiàng)工作而言,利用小孔和熔池區(qū)的紅外輻射來檢測激光焊接過程中出現(xiàn)的不同類型的缺陷,高幀頻紅外圖像將起著關(guān)鍵作用,它在整個(gè)過程中為缺陷檢測和分類提供了熱動(dòng)力學(xué)信息。
紅外傳感器描述
NIT公司制造的紅外傳感器在非制冷實(shí)時(shí)運(yùn)行時(shí)的幀速高達(dá)10kHz,檢測的波長為中波紅外,這在工業(yè)過程監(jiān)測中是一項(xiàng)突破,圖2為該傳感器的TACHYON1024CORE模塊。
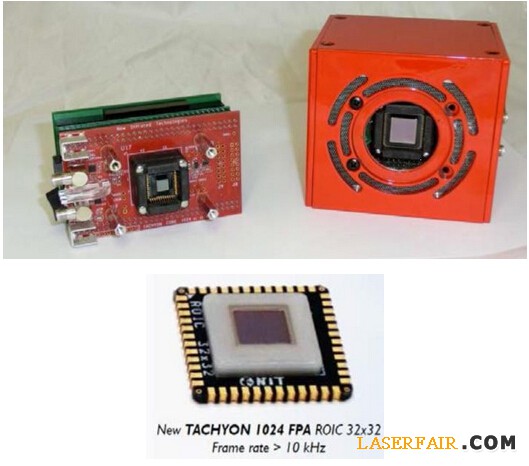
圖2 NIT公司的TACHYON1024CORE模塊:紅外相機(jī)和FPA
下表總結(jié)了TACHYON1024CORE模塊用于試驗(yàn)的主要參數(shù)。
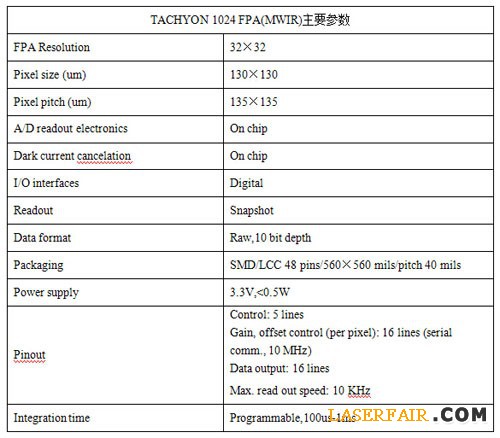
表1 TACHYON1024CORE用于試驗(yàn)的主要參數(shù)
TACHYON1024CORE模塊(見圖2)集成的傳感器是一個(gè)32×32像素的焦平面陣列(FPA),該FPA對中波紅外(MWIR)(1-5um)波長敏感,其參數(shù)總結(jié)在表2中。
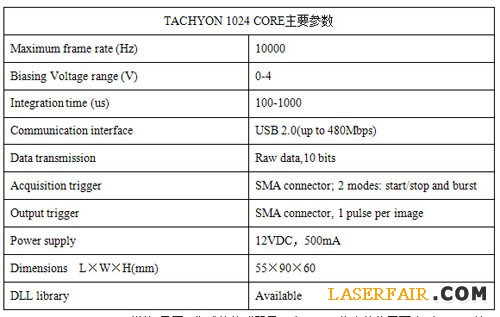
表2 TACHYON1024FPA(MWIR)用于試驗(yàn)的主要參數(shù)
激光頭和相機(jī)耦合
圖3顯示了NIT高速TACHYON1024CORE相機(jī)與激光束同軸布置的實(shí)驗(yàn)安裝,激光發(fā)射使用了4.4kW的RofinSinarNd:YAG激光器,該激光器波長為1.064um,激光束由安裝在ABB的6軸IRB6600機(jī)器人上的PermanovaWT03焊接頭發(fā)出。在本實(shí)驗(yàn)報(bào)告中,機(jī)器人的速度范圍為20-45mm/s,激光功率為2700-4000W。實(shí)驗(yàn)中涉及到搭焊的兩個(gè)不同鋅鍍層鋼片,厚度分別為0.8mm和1.5mm。
實(shí)時(shí)分類器
獲得激光焊接過程的熔池圖像,并在線分析圖像。圖4顯示了以2kHz幀速率獲得好的激光焊縫的紅外圖像,從中可以看出焊接過程中產(chǎn)生的飛濺物的密度。
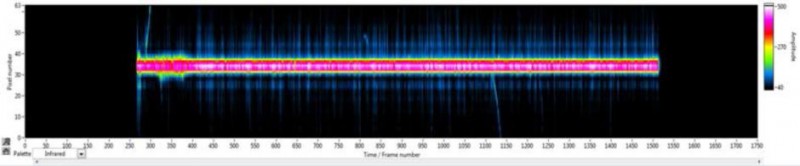
圖4 以2kHz幀速率獲得激光焊縫的紅外圖像,藍(lán)線代表焊接過程中產(chǎn)生的飛濺物
相機(jī)提供的原始圖像(即每秒2000幅圖像,每幅圖像1024個(gè)像素,每個(gè)像素10位)產(chǎn)生了大量的數(shù)據(jù),因此對大量圖像數(shù)據(jù)進(jìn)行降維是必要的。數(shù)據(jù)降維采用了主分量分析(PCA),該方法使用最大方差的正交分量的一個(gè)子空間來分解圖像的高維空間[8],僅保存原始圖像數(shù)據(jù)的四個(gè)主分量,這些分量表示具有最大方差的方向,這意味著利用PCA方法對圖像數(shù)據(jù)進(jìn)行降維得到的特征向量與熔池的幾何特征有關(guān)。圖像數(shù)據(jù)由1024個(gè)高壓縮到4個(gè)使得缺陷分類更快速,并對電腦的資源需求更少。
創(chuàng)建標(biāo)記缺陷的一個(gè)數(shù)據(jù)集來訓(xùn)練和測試檢測算法,該數(shù)據(jù)集由在焊接過程中得到的圖像生成,通過此來判別好的和有缺陷的接頭。首先,在最終標(biāo)記缺陷之前,樣品標(biāo)記上“OK”或“NOK”;其次,對“NOK”樣品進(jìn)行鑒定和標(biāo)記,辨別板間間隙(GAP)過大未焊透、板料變形(Deformation)未焊透、漏焊(Lack of weld)和開孔(Open Pore);最后,建立PCA主分量數(shù)組數(shù)據(jù)來訓(xùn)練系統(tǒng)(圖5顯示了分類結(jié)果實(shí)例)。
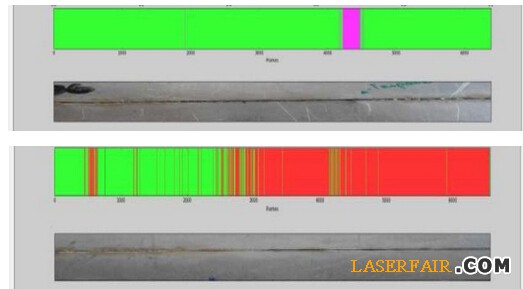
圖5 分類結(jié)果實(shí)例:“變形”和“間隙”
軟件開發(fā)從TACHYON傳感器獲得原始的圖像數(shù)據(jù),應(yīng)用PCA方法降維,為每幅焊接圖像生成一組新的數(shù)值,用K-最近鄰算法(KNN)[9]來分類這些值為OK或NOK。然后對NOK結(jié)果使用支持向量機(jī)(SVM)進(jìn)行重分類,這次分類為:“板間間隙”、“變形”、“漏焊”和“開孔”。
實(shí)驗(yàn)結(jié)果
通過對缺陷的鍍鋅鋼板接頭獲得有特征的中紅外圖像數(shù)據(jù)集,來評估缺陷檢測和分類。結(jié)果在表3中給出,第一列是缺陷的類型,以下TP(truepositives)代表正確,F(xiàn)P(falsepositives)代表誤報(bào),F(xiàn)N(falsenegatives)代表漏報(bào)。表3顯示一些缺陷分類失敗,大多數(shù)這些失敗在于缺陷類型之間混淆。
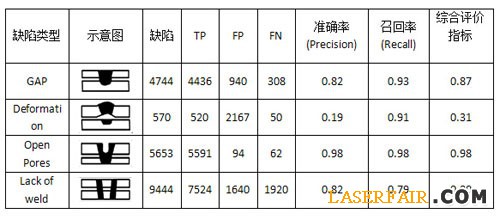
表3 不同缺陷類型檢測和分類結(jié)果
表4通過建立混淆矩陣揭示了這種解決方案的性能。缺陷的總數(shù)量為20411個(gè),檢測到的缺陷為20171個(gè)(98.8%的缺陷被檢測到)。比較表3和表4中的數(shù)字,僅10.4%的缺陷沒被正確分類,雖然有23.7%是誤報(bào),但是它們可以很容易地處理,因?yàn)樗鼈兛偸枪铝⒌某霈F(xiàn)。
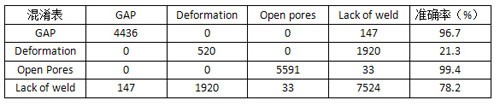
表4 混淆矩陣分類結(jié)果
總結(jié)
激光焊接是一種最常用的現(xiàn)代工業(yè)制造技術(shù),為了提高產(chǎn)品質(zhì)量,增加生產(chǎn)產(chǎn)量,基于激光加工過程開發(fā)更好的在線實(shí)時(shí)監(jiān)控系統(tǒng)是必要的。目前現(xiàn)有的大多數(shù)缺陷檢測系統(tǒng)工作需要設(shè)定合適的閾值,該閾值需要不斷地重復(fù)其過程來訓(xùn)練獲得,這在工業(yè)中是一個(gè)問題,部件老化、材料純度差異或維護(hù)問題是非均質(zhì)性常見來源,并且缺乏過程重復(fù)性。
本文提出了一種新的而經(jīng)濟(jì)的方法,該方法使得激光制造過程更加趨向靈活、高效、精確和零缺陷生產(chǎn)。已經(jīng)證明基于低成本、高速、非制冷中波紅外成像傳感器的機(jī)器學(xué)習(xí)解決方案能夠自動(dòng)識別和分類焊接缺陷,即使將傳感器安裝在不具有自適應(yīng)功能的標(biāo)準(zhǔn)激光頭上,大多數(shù)焊接缺陷都能夠被檢測出來,檢測成功率高達(dá)98.8%,對四種類型的缺陷進(jìn)行分類:板間間隙、變形、開孔和漏焊。在大多數(shù)情況下,建立與分類結(jié)果相應(yīng)的混淆矩陣可以得到很好的分類結(jié)果,僅10.4%的缺陷沒被正確分類。此外,系統(tǒng)的檢測和分類算法實(shí)現(xiàn)了檢測速率接近1kHz。
基于非制冷成像PbSe傳感器的紅外傳感技術(shù)開辟了更徹底控制系統(tǒng)一體化的途徑,該控制系統(tǒng)是基于紅外傳感器來監(jiān)測焊接過程質(zhì)量,以合理的價(jià)格應(yīng)用于未來的工廠。